The Benefits of Using Deformed Wire in Structural Applications
In this blog, you’ll learn more about the three primary benefits of using deformed wire in structural applications, such as bridges and retaining walls.
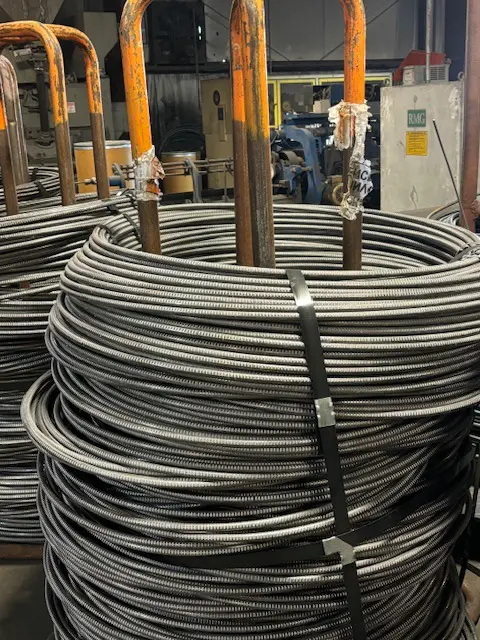
In this blog, you’ll learn more about the three primary benefits of using deformed wire in structural applications, such as bridges and retaining walls.
Welded wire reinforcement, including deformed bar anchors, gives concrete structures the strength to resist deformation caused by loads and temperature changes, but it can’t do this without carefully engineered wire deformations.
These deformations give the concrete something to “grip” onto, and their size, shape, position, and spacing determine how well the deformed wire performs. To avoid the additional work that would be needed if every deformed wire manufacturer developed their proprietary designs, ASTM has created specifications for deformed wire specifically used in structural applications, including A496 and A1064.
This blog looks at how deformed wire benefits structural applications. The three areas addressed are bond strength, tensile strength, and load distribution.
Concrete locks onto or grips deformed wire in two ways: 1) there is an adhesive or chemical interaction between the concrete and the wire, and 2) a mechanical interlocking where the concrete “keys-in” to the wire surface.
Increasing the surface area of the reinforcing wire provides more for the concrete to bond to. Larger diameter and non-round wire accomplish this to an extent, but forming indentations and/or protrusions along the surface, like those found on deformed bar anchors, has a bigger impact because they increase the surface area and mechanically interlock with concrete.
Bond strength is measured by pull-out or push-out tests, which measure the force needed to separate the concrete from the deformed wire.
Wire tensile strength stems from alloy composition plus the forming processes used. During deformation, dislocations or defects within the metal’s crystal structure move around and make further deformation more difficult, which increases strength and hardness. This is called work hardening or strain hardening. Deformation can also make grain boundaries smaller, which also inhibits dislocations. And, if the deformation process is performed at temperatures below the metal’s recrystallization temperature, the effects of work hardening are increased.
Because deformed wire has high tensile strength, this means it can support heavy loads without breaking or deforming, which is crucial in structural applications. Using larger-diameter wire or higher-strength steel, such as in deformed bar anchors, will also further increase load capacity for high-stress applications, such as bridges and retaining walls.
Deformed wire improves load distribution in concrete structures. This results from how the concrete “locks” into and grips the deformed wire, which helps spread the load along its length.
As is (or should be) well known, concrete is very strong in compression but weak in tension. Wire, however, is very strong in tension. Incorporating deformed wire into the concrete, therefore, provides both tensile and compressive strength while distributing the load throughout the structure. And, as mentioned earlier, deformed bar anchors have ridges and deformations that create mechanical interlocks with the surrounding concrete, increasing friction and improving load distribution, which in turn minimizes the risk of cracking or failure, prevents slippage, and reduces localized stress concentration.
Founded over 50 years ago, Fayette Custom Wire Products manufactures high-quality steel wire and rod, along with specialty metal wire products. Our deformed wire and bar anchors are produced to meet and exceed ASTM A496 and ASTM 1064 requirements.
Visit our blog for more wire forming resources, or contact us today to learn more about our capabilities.
©2025 Fayette Custom Wire Products, LLC